Have you ever wondered if your air compressor can still run even if it has a bad capacitor? This article will explore this topic and determine if a faulty capacitor can still allow your air compressor to function.
We will discuss the role of the capacitor, the signs of a bad capacitor, and whether or not it is safe to continue using your air compressor with a faulty capacitor. By the end, you’ll better understand how capacitors affect your air compressor’s operation.
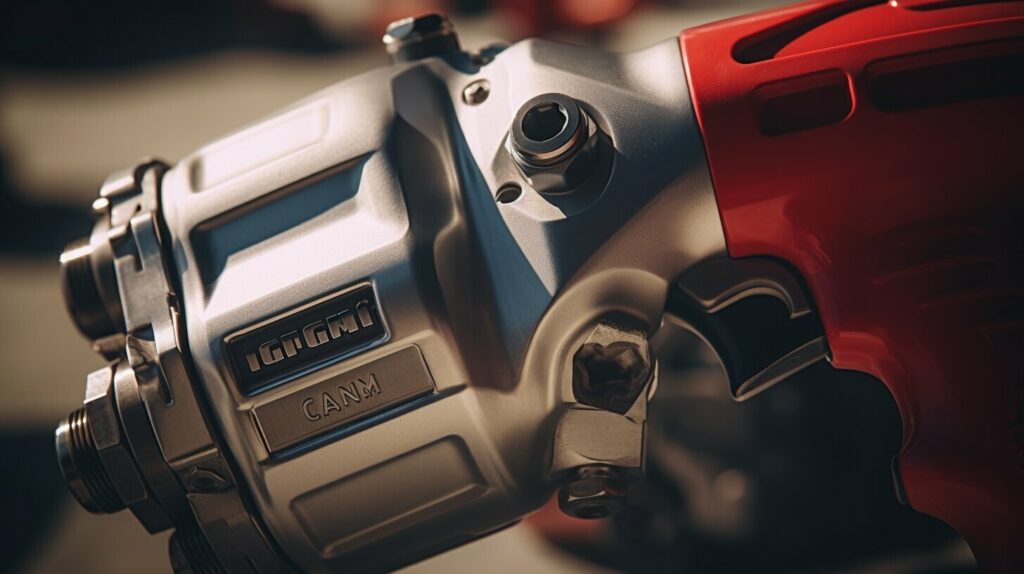
What is an Air Compressor
An air compressor is a versatile and essential tool used in various industries and applications, including construction, manufacturing, automotive, and more. It is a mechanical device that converts power, typically derived from electricity or gasoline, into potential energy stored in compressed air.
Definition of an Air Compressor
An air compressor consists of a motor, a compression system, and a storage tank. The motor powers the compression system, which draws air from the atmosphere and increases its pressure. The compressed air is then stored in the tank, ready for use in various pneumatic tools and equipment.
Types of Air Compressors
Various air compressors are available, each designed for specific needs and applications. The most common types include reciprocating air compressors, rotary screw air compressors, and centrifugal air compressors.
- Reciprocating air compressors use pistons to compress air, similar to how a car engine works. They are commonly used in small-scale applications and DIY projects.
- Rotary screw air compressors involve two helical screws that compress the air. These compressors are more efficient and are often used in commercial and industrial settings.
- Centrifugal air compressors use high-speed rotating impellers to accelerate the air and then decelerate it to create compressed air. These compressors are typically used in large-scale industrial applications.
Components of an Air Compressor
To understand the role of capacitors in air compressors, it’s essential to have a basic understanding of the main components of an air compressor.
- Motor: The motor powers the compression system and provides the initial energy required to start the compressor.
- Compression System: This component is responsible for drawing in air and compressing it to the desired pressure. It consists of valves, cylinders, pistons, and other related parts.
- Storage Tank: The tank stores the compressed air and acts as a reservoir for a continuous and steady air supply.
- Control Panel: The control panel allows the user to adjust settings, monitor pressure levels, and control the operation of the air compressor.
- Capacitors: Capacitors play a crucial role in the initial startup of the air compressor motor and provide auxiliary power for smooth operation.
Understanding Capacitors
Capacitors are electronic components commonly used in various electrical systems and machines, including air compressors. They store electrical energy temporarily and release it when needed. In air compressors, capacitors help start the motor and maintain a steady power supply during operation.
Definition of Capacitor
A capacitor is a passive electronic component that consists of two conductive plates separated by an insulating material called a dielectric. When a voltage is applied across the plates, it stores electrical charge, which can be discharged when required. Capacitors come in various types, sizes, and capacitance values depending on the specific application.
Functions of Capacitors
In air compressors, capacitors serve two primary functions:
- Starting the Motor: Air compressors, especially those with single-phase motors, require an extra power boost to overcome the initial inertia and start the motor. Capacitors store electrical charge and discharge it into the engine at startup, providing the necessary torque to get the motor running.
- Auxiliary Power Supply: During an air compressor’s operation, capacitors help stabilize the power supply. They provide auxiliary power and help maintain a smooth and steady flow of electricity to the motor, preventing voltage drops and power fluctuations.
Importance of Capacitors in Air Compressors
Capacitors are vital components of air compressors, especially for single-phase motors. The motor may struggle to start or exert sufficient torque to get the compressor running without capacitors. Capacitors ensure reliable startup and provide the necessary power for efficient and continuous operation.
Role of Capacitors in Air Compressors
Now that we understand the importance of capacitors in air compressors let’s delve deeper into their role and how they enable the smooth functioning of the compressor.
Starting Capacitor vs Running Capacitor
Two types of capacitors are commonly used in air compressors: starting capacitors and running capacitors.
- Starting Capacitor: As the name suggests, starting capacitors provide the initial power boost needed to start the motor. They have a higher capacitance value to deliver a significant surge of electricity during startup.
- Running Capacitor: On the other hand, running capacitors maintain a consistent power supply during the air compressor operation. They have a lower capacitance value and continuously deliver power to the motor, ensuring smooth and efficient operation.
How Capacitors Help Start the Air Compressor
When you switch on an air compressor, the starting capacitor releases a high-voltage electrical charge to the motor. This jolt provides the torque to overcome inertia and run the motor. Once the motor starts, the running capacitor takes over and provides a steady power supply to maintain operation.
Why Capacitors are Needed for Smooth Operation
Capacitors are essential for the smooth operation of air compressors, particularly those with single-phase motors. Without capacitors, the motor may fail to start or struggle during startup, leading to increased wear and tear, decreased efficiency, and a potentially shortened lifespan. Capacitors stabilize the power supply, prevent voltage drops, and ensure consistent performance.
Signs of a Bad Capacitor
Over time, capacitors can degrade and become faulty. It’s important to promptly identify and address any capacitor issues to prevent further damage to the air compressor. Here are some signs of a bad capacitor to watch out for:
Abnormal Noises
It could indicate a faulty capacitor if you hear unusual noises, such as humming or buzzing, from the air compressor during startup or operation. These noises are often accompanied by the motor struggling to start or running at reduced efficiency.
Inconsistent Compressor Operation
A malfunctioning capacitor can lead to erratic compressor operation. The compressor may start and stop abruptly, experience frequent motor tripping, or fail to start altogether. Inconsistent operation is a clear sign of capacitor problems that must be addressed.
Electrical Malfunctions
Faulty capacitors can cause electrical malfunctions in the air compressor. This can manifest as flickering lights, tripped circuit breakers, or other electrical issues. If you notice any electrical abnormalities while using the air compressor, it’s important to inspect the capacitors.

Effects of a Bad Capacitor on Air Compressor
A bad capacitor can adversely affect an air compressor’s performance, efficiency, and lifespan. Ignoring a faulty capacitor can lead to significant consequences. Here are some effects of a bad capacitor on an air compressor:
Reduced Efficiency
A malfunctioning capacitor can negatively impact the efficiency of an air compressor. The motor may struggle to start or operate at a lower speed, reducing productivity and performance. The inefficient operation can also result in higher energy consumption and increased costs.
Increased Energy Consumption
When a capacitor is not functioning correctly, the motor may draw excess power to compensate for the lack of auxiliary power. This increased power consumption can lead to higher energy bills and unnecessary strain on the electrical system.
Potential Damage to Compressor Motor
Continued use of an air compressor with a bad capacitor can cause damage to the motor. The motor may overheat, leading to premature wear and tear, decreased lifespan, and motor failure.
Additionally, the erratic power supply caused by a faulty capacitor can lead to voltage spikes, damaging other electrical components in the compressor.
Can the Air Compressor Run with a Bad Capacitor?
While it may be possible for an air compressor to run with a bad capacitor temporarily, it is not advisable. Running an air compressor with a faulty capacitor can exacerbate the existing issues and potentially cause further damage. Here’s what you need to know:
Temporary Operation without a Capacitor
In some cases, especially with small air compressors or systems with multiple capacitors, the compressor may start and run briefly without a capacitor. However, the motor will lack the necessary starting torque and auxiliary power supply, reducing efficiency and potential motor strain.
Long-Term Consequences
Continuously running an air compressor without a functioning capacitor can lead to severe consequences. The motor may overheat, experience increased wear and tear, and eventually fail, requiring costly repairs or replacement. Additionally, the lack of a steady power supply can affect the overall performance and efficiency of the compressor, leading to reduced productivity and increased energy consumption.
Safety Considerations
Operating an air compressor with a bad capacitor can also pose safety risks. A faulty capacitor can cause electrical malfunctions, leading to potential shock hazards or fire hazards. It’s crucial to prioritize safety and address capacitor issues promptly.
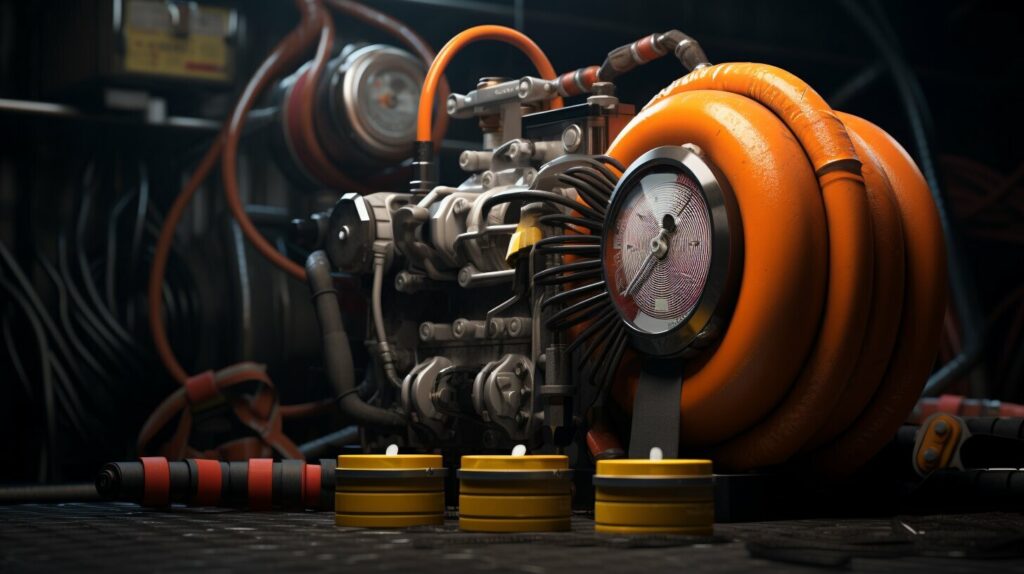
Steps to Replace a Bad Capacitor
If you suspect your air compressor has a faulty capacitor, it’s important to replace it immediately. Here are the steps to replace a bad capacitor:
Identifying the Faulty Capacitor
First, you’ll need to identify the faulty capacitor. The capacitors are typically located in the control panel of the air compressor. Inspect the capacitors for any signs of damage, such as bulging or leaking. You can also use a multimeter to test the capacitance and check for continuity.
Sourcing the Correct Replacement
Once you’ve identified the faulty capacitor, you must source a replacement. Consult the air compressor’s manual or the manufacturer to determine the required specifications and capacitance value. Using the correct replacement capacitor is important to ensure compatibility and optimal performance.
Installation Process
To replace the capacitor, disconnect the power supply to the air compressor. Carefully remove the faulty capacitor, taking note of its wiring connections. Install the replacement capacitor, ensuring proper wiring connections and secure placement. Double-check all the connections, reassemble the control panel, and restore the power supply.
Preventive Maintenance for Capacitors
Regular preventive maintenance is crucial to prolong the lifespan and ensure the optimal performance of capacitors in air compressors. Here are some maintenance practices to consider:
Regular Inspection
Periodically inspect the capacitors for any signs of damage, including bulging, leaking, or loose connections. Regular visual inspections can help detect issues early and prevent further damage to the air compressor.
Cleaning and Maintenance
Keep the capacitors and the surrounding area clean from dust, debris, or potential contaminants. Regularly clean the control panel and ensure proper ventilation to prevent overheating. In addition, check the capacitors’ terminal connections to ensure they are clean and secure.
Annual Capacitor Replacement
As a preventive measure, consider replacing the capacitors annually. Over time, capacitors can degrade, even if they appear to function correctly. Annual replacement can help mitigate potential issues and ensure optimal performance.
Seeking Professional Help
While individuals with electrical knowledge and experience can address some capacitor-related issues, it’s often best to seek professional help. Here’s when you should consider consulting a technician:
When to Consult a Technician
If you are unsure about the capacitor replacement process or if the air compressor experiences persistent issues despite capacitor replacement, it’s advisable to consult a technician. A trained professional can diagnose the problem accurately, address any underlying issues, and ensure safe and proper repairs.
Choosing a Reliable Service Provider
When seeking professional assistance, choose a reliable service provider with experience in air compressor maintenance and repairs. Look for certifications, positive customer reviews, and a strong reputation in the industry. A trustworthy technician will help diagnose and resolve capacitor-related issues efficiently.
Benefits of Professional Assistance
Professional help offers several benefits, including expert knowledge and accurate diagnosis of capacitor problems. Technicians can identify any additional issues impacting the compressor’s performance and make the necessary repairs.
Additionally, professional assistance ensures safety, preventing potential hazards associated with electrical components.
Conclusion
In conclusion, a bad capacitor can significantly affect an air compressor’s performance, efficiency, and lifespan. Capacitors are crucial in starting the motor and maintaining a steady power supply during operation.
Understanding the signs of a bad capacitor and addressing the issue promptly is essential to prevent further damage and ensure safe and efficient operation. Regular preventive maintenance, including inspection, cleaning, and annual capacitor replacement, can help prolong the life of capacitors and maintain optimal compressor performance.
When in doubt, consult a professional technician to address any capacitor-related issues and ensure the safety and reliability of your air compressor.
Jennifer is a seasoned mechanical engineer with a passion for precision and innovation. After graduating from Caltech, Jane has dedicated over a decade to the intricate world of air compressors. As a lead test engineer at Pneumatic Performance Labs, she is pivotal in assessing air compressors’ efficiency, safety, and performance. Her meticulous approach has enhanced numerous compressor models, ensuring they meet the highest industry standards.