Welcome to our guide on safety precautions for air compressors. Whether you’re a professional or a hobbyist, using air compressors can be helpful. However, it’s essential to prioritize safety to prevent potential injuries and equipment damage.
This section will discuss the importance of regular inspection, proper training, and appropriate equipment to ensure air compressors’ safety. We will also provide a brief overview of what will be covered in the remaining sections of the article so you know what to expect.
Safety Precautions When Using Air Compressors: Inspection, Training, and Equipment
Air compressors are versatile tools used in various industries for various applications. However, they also present potential hazards that can cause serious injuries or property damage. Ensuring air compressors’ safety should be a top priority for any worker or organization that utilizes these tools. This section will discuss the importance of regular inspection, proper training, and appropriate equipment when operating air compressors.
The Importance of Air Compressor Inspection
Regular inspections of air compressors are essential for identifying potential safety hazards and ensuring proper functioning. Inspections include a comprehensive check of the equipment, including the hoses, valves, and regulators, to ensure they are in good condition. The pressure relief valve should be inspected and tested to ensure it functions correctly.
During inspections, look for loose or damaged electrical connections and broken or frayed hoses. Proper and periodic inspection reduces the likelihood of accidents or equipment failure. It is advisable to perform inspections at regular intervals and after any significant repairs or changes to the equipment.
It’s important to note that visual inspections of air compressors may not be enough to detect certain hazards. In such cases, Non-Destructive Testing (NDT) techniques such as Ultrasonic testing and Magnetic Particle testing may be necessary to identify invisible cracks or defects to the naked eye. Training in NDT techniques is highly recommended for workers who operate air compressors regularly.
Safety Precautions When Using Air Compressors: Inspection, Training, and Equipment
When it comes to working with air compressors, safety should always be a top priority. Proper inspection, training, and equipment are essential for minimizing the risk of accidents and ensuring a safe working environment. This section will explore the importance of proper training for air compressor use and recommend training resources.
Proper Training for Air Compressor Use
While air compressors are valuable tools, they can also be dangerous when used incorrectly. Proper training is essential for using air compressors safely and preventing accidents. It is important to note that training should not be a one-time event but an ongoing process to ensure all employees are up to date on safety guidelines.
One of the most critical aspects of training is understanding the functions and components of the air compressor. This includes operating the compressor controls and removing and attaching hoses and fittings. Workers should also be trained to identify and avoid potential equipment hazards, such as overloading the compressor or exposing themselves to compressed air.
Several resources are available for air compressor safety training, including online courses, instructional videos, and on-site training programs. Employers should ensure that employees receive adequate training before operating air compressors and participate in ongoing training to stay up-to-date with safety standards and regulations.
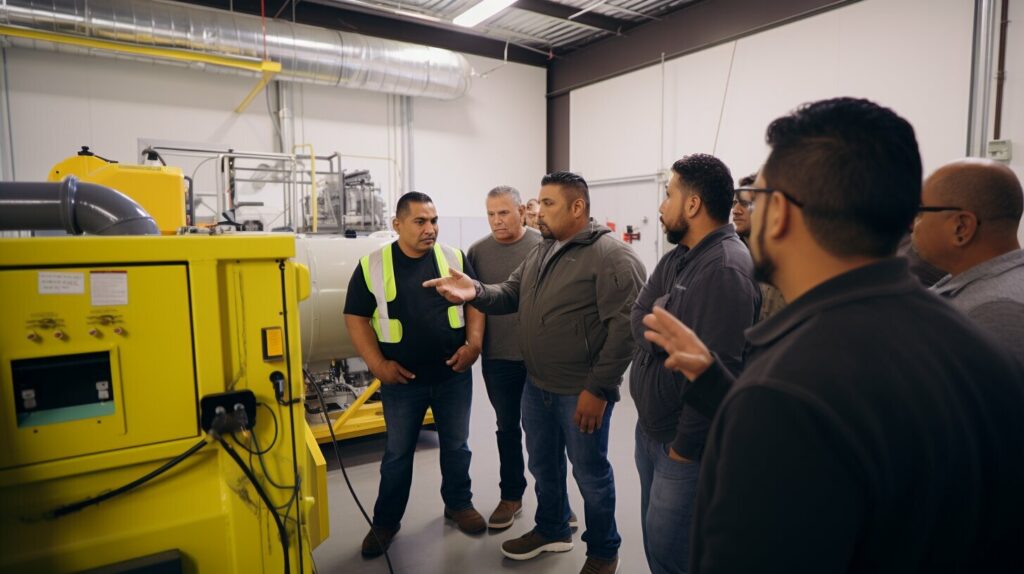
“Proper training is essential for using air compressors safely and preventing accidents.”
In addition to formal training programs, employers should encourage workers to ask questions and seek clarification on any safety concerns. This open communication can help identify potential hazards and prevent accidents from occurring.
Overall, investing in proper training for air compressor employees is essential in ensuring a safe working environment and preventing accidents.
Choosing the Right Equipment for Air Compressor Safety
When using air compressors, having the right safety equipment is essential. It protects you from potential hazards and ensures you’re working in compliance with safety regulations. Below are some of the key types of safety equipment that you should consider:
Equipment | Description |
---|---|
Protective Gloves | Protective gloves are a must-have when working with air compressors. They protect your hands from pinches, cuts, and abrasions and provide a better grip on tools and equipment. |
Protective Eyewear | Protective eyewear is necessary when working with air compressors to prevent eye damage from flying debris, dust, or other particles. |
Earplugs | Earplugs protect your ears from loud noise produced by air compressors. Long-term exposure to high noise levels can cause permanent hearing loss. |
Respirators | Respirators protect workers from inhaling hazardous materials, such as fumes, dust, or mold spores, during air compressor use. |
Safety Shoes | Safety shoes protect your feet from falling objects and provide better traction on slippery surfaces. |
Choosing the appropriate safety equipment is important based on the type of air compressor you’re using and the hazards of the specific application. For example, if you’re working with chemicals, you may need a respirator, while working with pneumatic tools may require protective gloves and eyewear.
Additionally, you should always follow safety guidelines when using the equipment. Don’t remove safety guards or disable safety devices on the air compressor. Always turn off and unplug the compressor before making any adjustments or repairs.
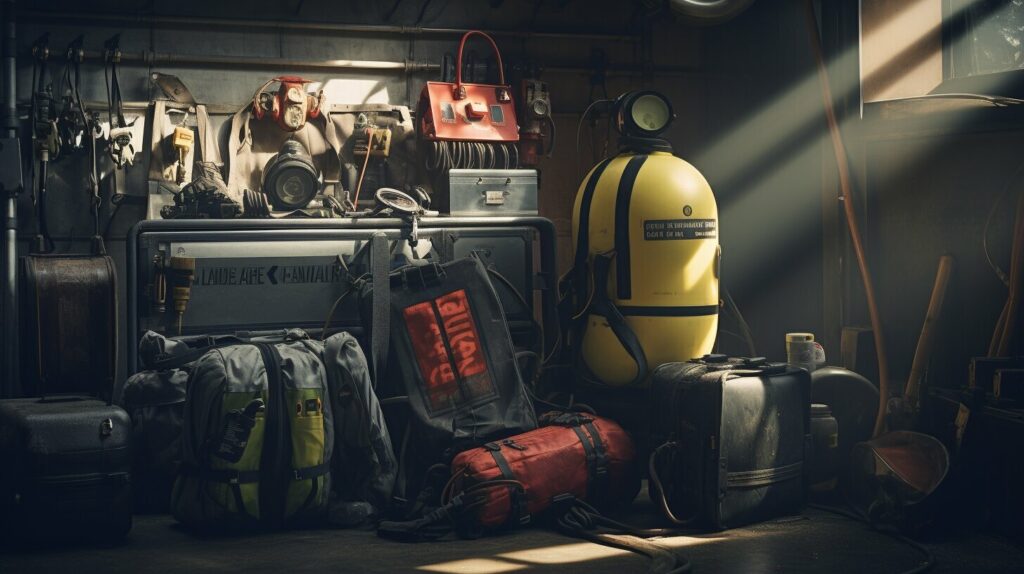
Understanding Air Compressor Safety Procedures
When using air compressors, it is important to follow proper safety procedures to minimize the risk of accidents and injuries. Here are some essential guidelines to ensure safe operation:
- Proper Setup: Ensure the air compressor is on a stable, level surface and secured to prevent tipping. Please keep it away from heat sources, moisture, and flammable materials.
- Ventilation: Ensure proper ventilation in the workspace to prevent the buildup of hazardous fumes or gases. Use a proper ventilation system or open windows and doors to allow fresh air to circulate.
- Electrical Safety: Follow all electrical safety guidelines, including using properly grounded outlets, inspecting cords and plugs for damage, and avoiding contact with electrical components when hands or feet are wet.
- Compressed Air Handling: Do not point compressed air at yourself or others; it can cause serious injury or death. Use appropriate air hoses and connectors and ensure that they are properly secured.
Additionally, adhering to air compressors’ safety standards and regulations is essential. Familiarize yourself with relevant guidelines and remember them during operation to ensure a safe and efficient working environment.
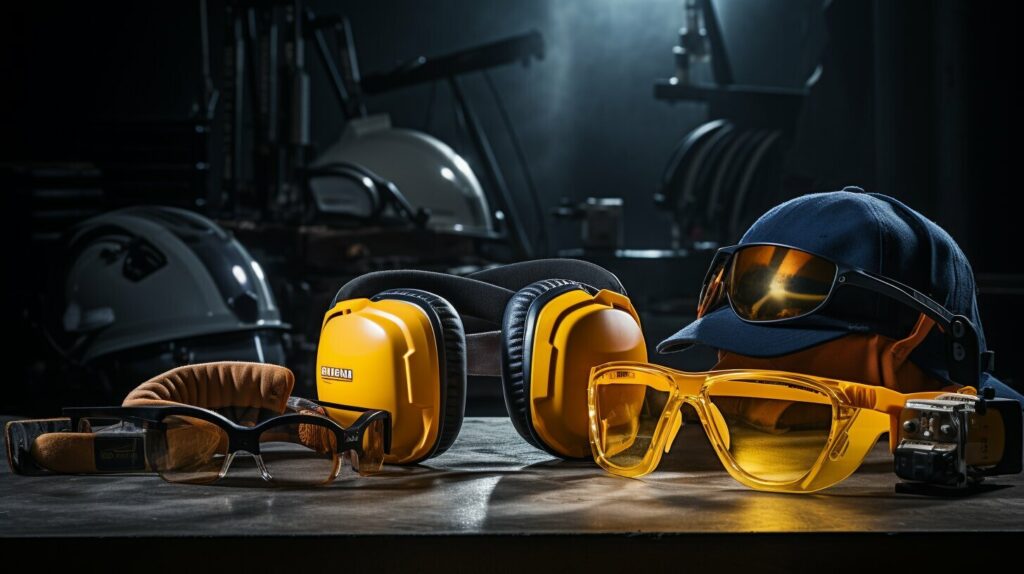
Tip: Keep a safety checklist handy and conduct regular inspections to ensure that all safety measures are in place and functioning properly.
Safe Operation of Air Compressors
Proper operation of air compressors is critical to ensuring the safety of both the operator and the equipment. By exercising caution and following best practices, accidents and equipment damage can be avoided.
Start-up and Shut-down Procedures
Following the manufacturer’s instructions is essential when starting up an air compressor. Operators should ensure that all connections are secure and that the electrical system is functioning correctly. After starting, monitor the pressure gauge until the compressor has reached its desired operating pressure.
When shutting down the compressor, operators must turn off the power before closing all valves and releasing any pressure within the system. The equipment should not be left unattended until the pressure has been fully released.
Monitoring Pressure Levels
Monitoring the pressure levels in an air compressor system is essential to ensure safe operation. Operators should regularly check the pressure gauges and adjust the regulator as needed to maintain an appropriate operating pressure. Overloading the system can lead to accidents and damage to the equipment.
Avoid Overloading the Compressor
Overloading the air compressor can cause severe damage to the equipment and create hazardous conditions for the operator. Operators should avoid exceeding the recommended operating pressure and regularly check the load placed on the compressor to ensure that it’s not overloaded.
Handling Compressed Air Hoses Safely
Compressed air hoses must be handled with care to avoid accidents. Operators should inspect hoses regularly for signs of damage or wear and avoid bending or crimping them. When disconnecting a hose, the operator must release the pressure within the system before removing it to prevent it from whipping dangerously.
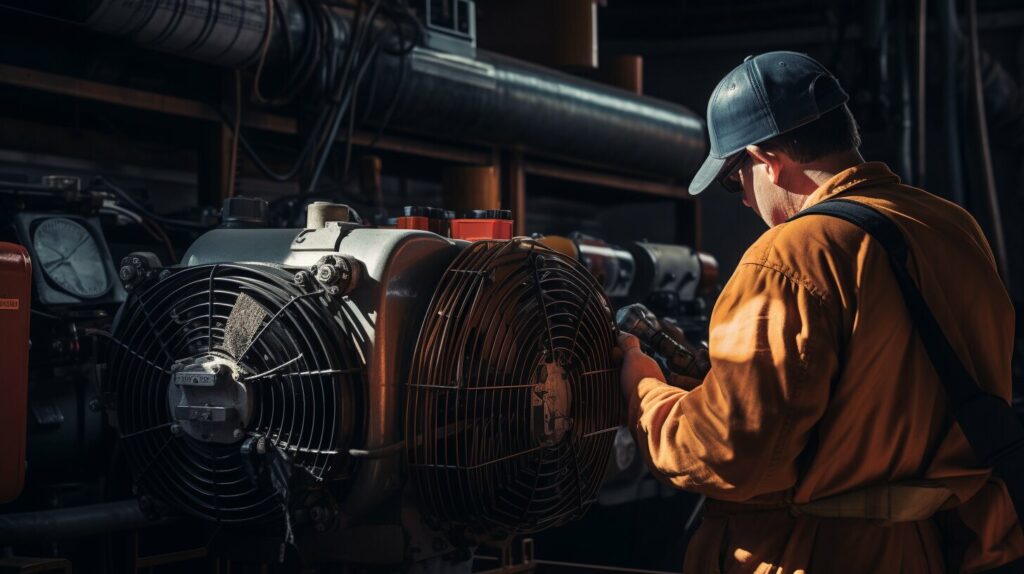
Regular Maintenance for Air Compressor Safety
Regular maintenance is essential for ensuring the safety of air compressor operation. By performing routine maintenance tasks, you can reduce the risk of equipment failure, prevent accidents, and prolong the life of your compressor. Here are some key maintenance tasks that should be performed regularly:
Task | Frequency |
---|---|
Check for leaks | Weekly |
Clean or replace filters | Monthly |
Check oil level and quality | Daily |
Lubricate moving parts | Monthly |
Tighten bolts and fittings | Quarterly |
Always refer to the manufacturer’s instructions for your specific compressor model when performing maintenance tasks. It’s also important to follow proper safety procedures while performing maintenance, such as wearing appropriate personal protective equipment (PPE) and making sure the compressor is turned off and depressurized before beginning.
Regular maintenance not only helps ensure safety but also improves the efficiency and performance of your compressor. Keeping your compressor in top condition can save money on energy costs and prevent costly breakdowns.

Safety Issues and Solutions When Using Air Compressors
While air compressors can be useful for various tasks, they pose potential safety hazards. By understanding the common safety issues that may arise, you can take steps to prevent accidents and injuries. Here are some safety issues and solutions when using air compressors:
Issue | Solution |
---|---|
Overheating | Use appropriate safety equipment and follow proper handling procedures for compressed air. Avoid using compressed air to clean skin or clothing; never point the air stream at another person. |
Oil Contamination | Regularly check and change the oil as needed. Use the recommended type of oil for your compressor. |
Excessive Noise | Wear ear protection and consider using noise-reducing equipment, such as a silencer or acoustic enclosure. Inspect the compressor for loose or worn parts that may cause excess noise. |
Compressed Air Hazards | Use appropriate safety equipment and follow proper handling procedures for compressed air. Avoid using compressed air to clean skin or clothing, and never point the air stream at another person. |
By addressing these common safety issues, you can ensure your air compressor’s safe and effective use.
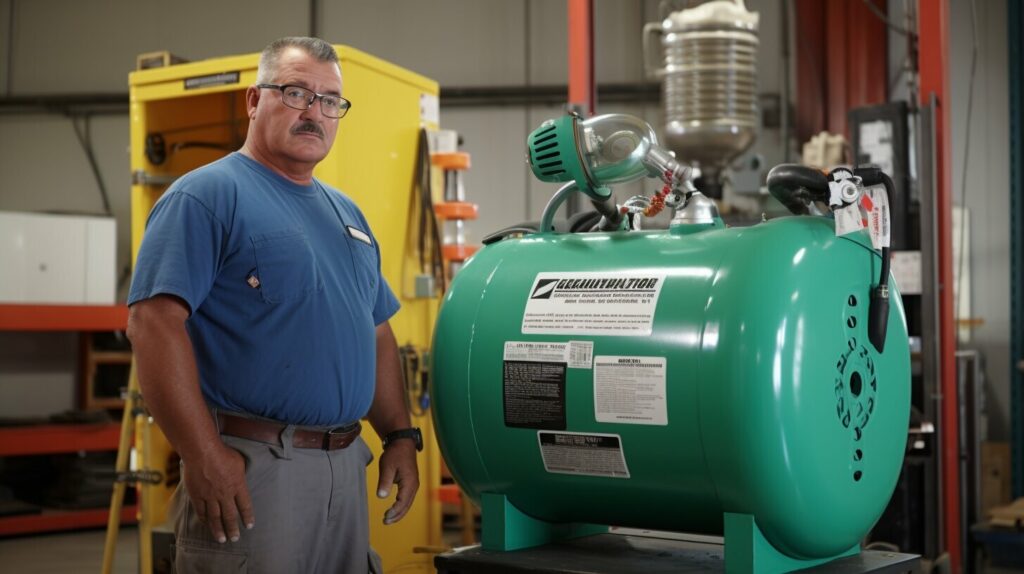
“It is crucial to address safety issues when using air compressors. By taking preventative measures, you can ensure safe and efficient use of this equipment.”
Safeguarding Your Workspace: Ensuring a Safe Working Environment with Air Compressors
When it comes to operating air compressors, creating a safe working environment is crucial for preventing accidents and ensuring the well-being of employees. Here are some essential safety measures to consider:
Factor | Importance |
---|---|
Proper Ventilation | Good ventilation is essential to prevent the buildup of carbon monoxide and other toxins in the workspace. Ventilation should be provided through open windows, fans, or air conditioning systems. |
Adequate Lighting | Effective communication among employees is essential for promoting safety in the workplace. Employees should be made aware of the potential hazards of air compressor operation and trained on proper safety procedures. |
Clean Workspace | Employees should be able to see the compressor and all related equipment clearly. Adequate lighting can help prevent accidents caused by inadequate visibility. |
Communication and Awareness | Effective communication among employees is essential for promoting safety in the workplace. Employees should be made aware of the potential hazards of air compressor operation and trained on proper safety procedures. |
Implementing these measures can go a long way in creating a safe work environment and preventing accidents. It is important to regularly assess the workspace for potential hazards and address any issues to maintain a safe work environment.
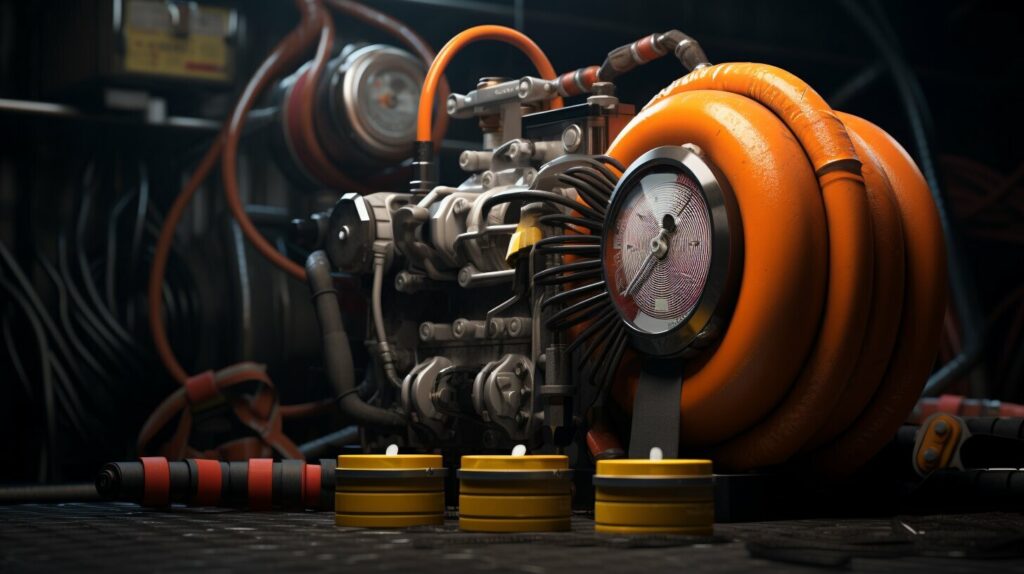
“A clean workspace is crucial to ensure that employees can move freely and without obstruction.”
Emergency Preparedness for Air Compressor Accidents
Quick and appropriate action is crucial to minimize potential injuries and property damage in an air compressor accident or emergency. Here are some guidelines to follow:
Step | Action to Take |
---|---|
1 | Shut off the power source immediately if there is an electrical malfunction, or turn the compressor off in case of any other issue. |
2 | Evacuate the area and move to a safe location, ideally out of the building and away from the compressor. |
3 | If there are any injured persons, provide first aid and call for emergency medical assistance. Avoid moving the person unless necessary. |
4 | If a fire occurs, use fire extinguishers or other appropriate methods to put out the flames. Do not use water on electrical fires. |
5 | Notify the relevant authorities and follow their instructions regarding reporting the incident, managing the site, and conducting any necessary investigations. |
Always prioritize safety and be prepared to act quickly in an emergency. Conduct regular safety drills and ensure all workers know emergency procedures.

Safeguarding Your Workplace: Promoting a Safety Culture in Air Compressor Use
Creating a safety culture in the workplace is crucial for ensuring the well-being of employees and maintaining a safe working environment. This is particularly important for workplaces that utilize air compressors, as the risks associated with their use can be significant. But how can you promote a safety culture in your workplace?
Here are some practical tips to help you create a culture of safety:
Encourage Employee Engagement
Employee participation is key to fostering a strong safety culture. Encourage your employees to take an active role in identifying potential hazards and developing safety procedures. Provide opportunities for feedback and suggestions, and take employee concerns seriously. By involving your workforce, you can create a sense of ownership and investment in safety practices, making them more likely to follow through.
Provide Ongoing Training and Awareness Programs
Regular training and awareness programs can help employees stay informed about safety procedures, updates, and new equipment or processes that may affect their safety. Ensure all employees receive appropriate training before using air compressors and provide refresher courses periodically. Keeping your workforce informed and up-to-date can help mitigate risks and prevent accidents.
Lead by Example
Leadership plays a critical role in promoting a safety culture. Leaders should model safe behavior, follow established safety procedures, and prioritize safety over other concerns. By consistently demonstrating a commitment to safety, leaders can set the tone for the entire workplace and encourage employees to follow suit.
Implement Continuous Improvement Processes
Safety culture is not a static concept but an ongoing process. Encourage employees to identify improvement areas and provide regular feedback and evaluation opportunities. By continually striving to improve safety practices and procedures, you can create a workplace with a culture that prioritizes and supports safety.
With these tips, you can create a safety culture that prioritizes the well-being of your employees and promotes a safe and healthy working environment.
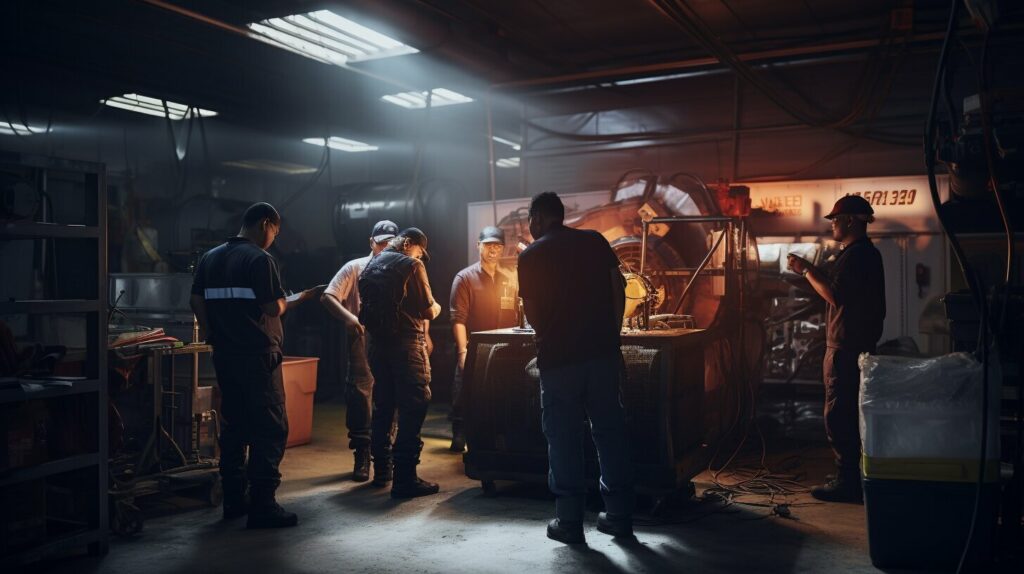
Safety FAQ: A Comprehensive Guide to Air Compressor Safety
As with any equipment, air compressors require proper handling and maintenance to ensure safety. Here are some frequently asked questions about air compressor safety:
Can compressed air cause injury?
Yes, compressed air can cause serious injuries if not handled properly. Never point compressed air at yourself or others, as it can cause damage to the skin, eyes, and internal organs. Always wear appropriate safety gear, such as goggles and ear protection when using compressed air.
How often should air compressors be inspected?
Air compressors should be inspected regularly, ideally before each use. At a minimum, they should be inspected monthly to ensure proper functioning and identify potential hazards. Following the manufacturer’s recommended maintenance schedule and documenting all inspections is important.
What safety measures should be taken when using air compressors?
Proper training, appropriate safety gear, and adherence to safety procedures are crucial when using air compressors. Workers should always wear protective gear, such as goggles and gloves, and follow safe operating procedures, such as proper start-up and shut-down procedures and monitoring pressure levels. Adequate ventilation and lighting are also essential for a safe working environment.
How can I prevent the air compressor from overheating?
Air compressor overheating can be prevented by ensuring proper airflow and ventilation, keeping the compressor clean, and checking for leaks. Overheating can also be caused by overloading the compressor or running it for extended periods without proper rest. Always follow the manufacturer’s recommended operating instructions and shut down the compressor if it becomes too hot.
What should I do in case of an air compressor emergency?
In an air compressor emergency, workers should immediately shut down the compressor and follow appropriate procedures. This may include releasing pressure from the system, cutting off power, and calling for necessary medical assistance. It’s important to have a clear emergency response plan and regularly train workers on how to respond in an emergency.
How can I promote a culture of safety in my workplace?
Promoting a culture of safety requires a commitment to ongoing training and education, open communication among workers, and continuous improvement in safety practices. Workers should be encouraged to report any safety hazards or concerns and rewarded for following safe practices. Regular safety meetings and training sessions can also help promote a culture of safety in the workplace.
Are there any safety regulations or standards for air compressor use?
Safety regulations and standards, such as OSHA regulations, govern air compressor operation and maintenance. Workers should be familiar with and adhere to these regulations to ensure a safe working environment. Employers should also regularly review and update their safety policies to stay current with industry standards and best practices.
Sources
- Cleaner production in a remanufacturing process of air compressors by Javier Esquer, Jose Angel Arvayo, Clara Rosalia Alvarez-Chavez, Nora Elba Munguia-Vega & Luis Velazquez, published in the International Journal of Occupational Safety and Ergonomics, Volume 23, 2017 – Issue 1. This article discusses cleaner production in the remanufacturing process of air compressors.
- Experimental and numerical analysis of the performance of the R290 rotary compressor used in a split-room air conditioner at high ambient temperature by Jian Hua Wu, Hong Yan Shi, Shuai Zhang, Jia Chen Li, Bo Wen Lei & Yan Jun Du, published in Science and Technology for the Built Environment, Volume 27, 2021 – Issue 2. This article presents an experimental and numerical analysis of the performance of a specific type of air compressor.
- Latest practical notes and recent lessons learned on reciprocating compressors by Amin Almasi, published in the Australian Journal of Mechanical Engineering, Volume 14, 2016 – Issue 2. This article provides practical notes and lessons learned on reciprocating compressors.