I. Introduction
Air compressors are commonly used in various industries and applications, from manufacturing and construction to automotive repair and maintenance. Understanding how an air compressor works can help you appreciate its importance and how it can be used effectively in different settings.
Overview of air compressors
An air compressor is a device that converts power, typically from an electric motor or a gas engine, into compressed air. It works by compressing the air and storing it in a tank, which can then be used for various applications.
The basic components of an air compressor include:
Motor: The motor provides the power needed to operate the compressor. It can be an electric motor or a gas engine, depending on the type of compressor.
Compression system: The compression system consists of a pump or a compressor unit that draws in air and compresses it to a higher pressure.
Tank: The tank is where the compressed air is stored. It acts as a reservoir, allowing for a steady supply of compressed air when needed.
Controls and safety features: Air compressors have various controls and safety features, such as pressure gauges, pressure switches, and relief valves, to ensure safe and efficient operation.
Importance and applications of air compressors
Air compressors play a crucial role in many industries and applications due to their ability to generate and store compressed air. Some of the key reasons why air compressors are important include:
Powering pneumatic tools: Air compressors are commonly used to power pneumatic tools, such as impact wrenches, nail guns, and spray guns. Compressed air provides the necessary force and pressure for these tools to function effectively.
Industrial applications: Air compressors are widely used in industrial settings for
manufacturing, assembly line operations, and construction. They power machinery, control, and pneumatic systems, making them essential for many industrial processes.
Automotive industry: Air compressors are extensively used in the automotive industry for tire inflation, painting, and operating pneumatic tools in repair shops and car manufacturing plants.
HVAC systems: Air compressors are crucial in heating, ventilation, and air conditioning (HVAC) systems. They are used to power air conditioning units, refrigerators, and other cooling systems.
Cleaning and maintenance: Air compressors are used for cleaning applications, such as removing dust and debris, and maintenance tasks like blowing out air filters and drying surfaces.
Understanding how an air compressor works and its various applications can help you make informed decisions when choosing and using it for your specific needs.
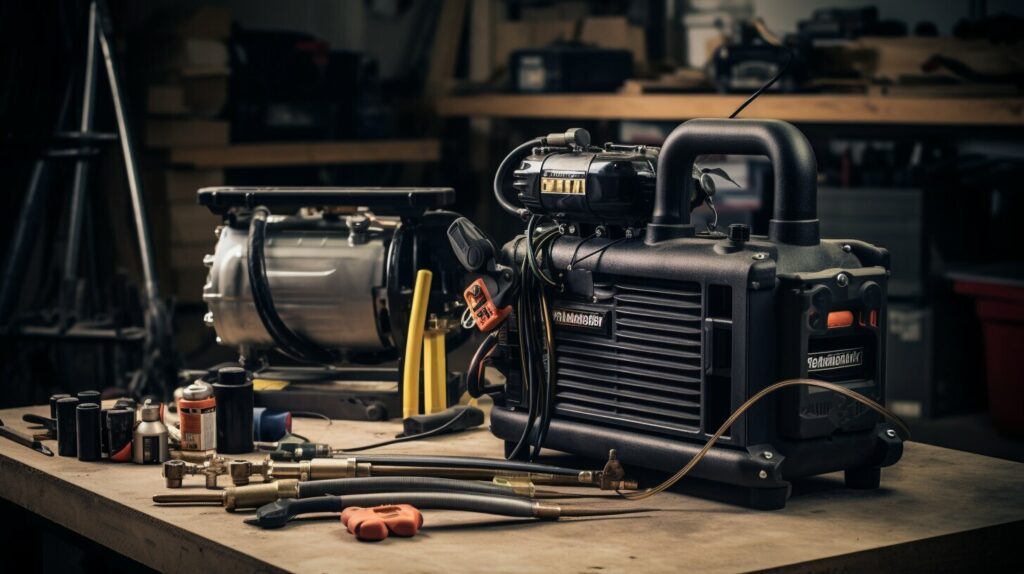
II. Basic Components of an Air Compressor
An air compressor is a powerful tool that converts power from an electric motor or engine into kinetic energy stored in pressurized air. Understanding the basic components of an air compressor can help you grasp how it works. Here are the main parts:
Air compressor pump: The pump is the heart of the air compressor. It draws in air and compresses it, increasing the pressure and storing it in a tank for later use. There are different types of pumps, such as reciprocating, rotary screw, and centrifugal, each with its own advantages and applications.
Pressure switch: The pressure switch is responsible for turning the compressor on and off to maintain the desired pressure level in the tank. It operates by sensing the pressure and triggering the motor or engine to start or stop when it reaches a certain set point.
Pressure relief valve: The pressure relief valve is a safety device that ensures the compressor does not exceed its maximum rated pressure. If the pressure in the tank becomes too high, the relief valve opens, releasing the excess tension and preventing damage to the compressor or other connected equipment.
By understanding these basic components, you can better appreciate how an air compressor operates and how it can be used in various applications.

III. Working Principle of an Air Compressor
An air compressor is a mechanical device that converts power from an electric motor, diesel engine, or gasoline engine into potential energy stored in compressed air. Let’s take a closer look at the working principle of an air compressor and its different stages:
Compression stage
The compression stage is the first step in the air compression process. The air intake valve opens when the compressor is turned on, and outside air is pulled into the compression chamber. The piston, driven by the motor, moves downward and compresses the air, reducing its volume and increasing its pressure. This compressed air is then discharged into a storage tank.
Exhaust stage
Once the air is compressed and reaches the desired pressure, the air compressor goes into the exhaust stage. The exhaust valve opens, allowing the compressed air to flow from the storage tank to the desired application or tool. The air pressure is maintained within a specific range, ensuring the continuous operation of the tool or equipment connected to the compressor.
Intake stage
As the compressed air is used and the pressure in the storage tank decreases, the intake stage comes into play. The intake valve opens, drawing in fresh air from the environment to refill the storage tank. This intake air undergoes the compression process again to maintain the desired pressure level.
Cooling stage
During the compression process, the air temperature increases significantly. A cooling stage is included to prevent damage to the compressor and its components. Air compressors are equipped with a cooling mechanism, such as a radiator or an intercooler, to reduce the temperature of the compressed air before it enters the storage tank. This cooling process helps to improve efficiency and extend the lifespan of the air compressor.
Understanding the working principle of an air compressor is essential for its proper operation and maintenance. Whether it’s for industrial applications or personal use, air compressors play a vital role in various industries and tasks.
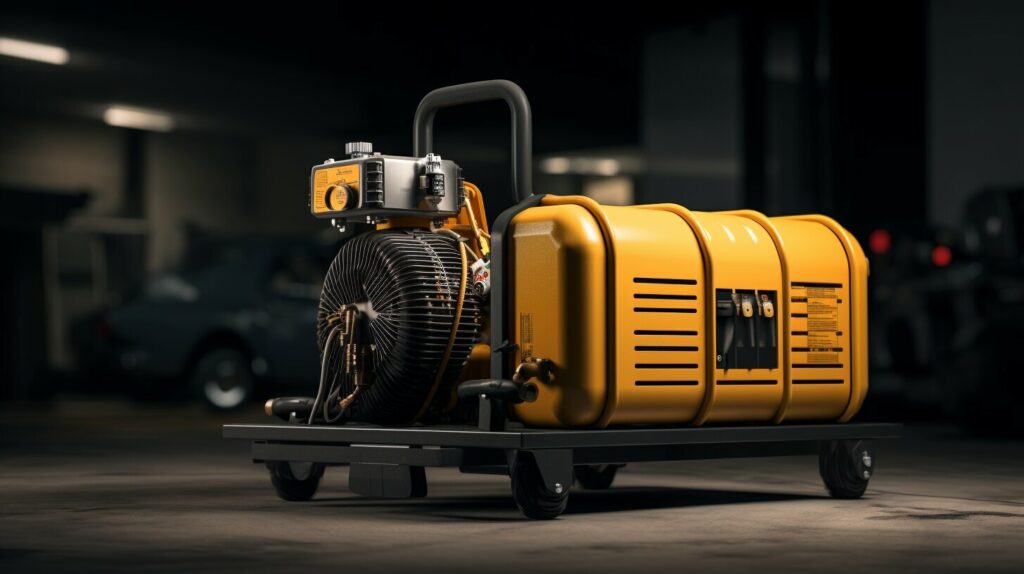
IV. Types of Air Compressors
Different types of air compressors are available, each with unique mechanisms and applications. Here are some of the most common types:
Reciprocating air compressors
Reciprocating air compressors, also known as piston compressors, work by using a piston and cylinder arrangement. They use a motor to drive the piston, compressing the air and storing it in a tank. Reciprocating compressors can be either single-stage or two-stage, with two-stage compressors providing higher pressure output.
Rotary screw air compressors
Rotary screw air compressors consist of two rotating helical screws, also known as rotors. These rotors trap and compress the air as they turn, creating a continuous air flow. The compressed air is discharged into a storage tank or directly to the application. Rotary screw compressors are known for their efficiency, reliability, and continuous operation capabilities.
Centrifugal air compressors
Centrifugal air compressors use a high-speed rotating impeller to accelerate and push the air outward. As the air moves through the impeller, it gains kinetic energy, converted into pressure energy. Centrifugal compressors are commonly used in large industrial applications, such as power generation and manufacturing.
Different types of air compressors have advantages and limitations, and the choice depends on the application’s specific requirements. Understanding how each compressor works helps select the right one for the task.
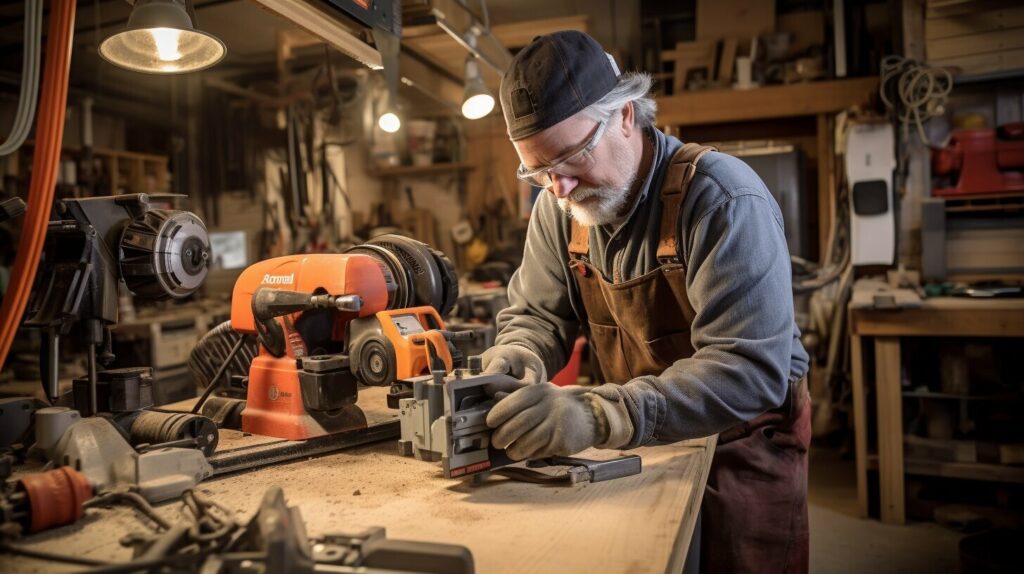
VI. Maintenance and Safety Tips
Regular maintenance procedures
To keep your air compressor running smoothly and efficiently, it’s important to follow regular maintenance procedures. Here are some tips to help you maintain your air compressor:
1. Check oil levels: If your air compressor is oil-lubricated, check the oil levels regularly. Low oil levels can cause increased friction and wear on the compressor’s internal components. You should also change the oil according to the manufacturer’s recommendations.
2. Clean or replace air filters: The air filters in your compressor are responsible for keeping out dust and debris. Over time, these filters can become clogged and restrict airflow. It’s important to clean or replace them regularly to ensure proper operation.
3. Inspect belts and hoses: Check the belts and hoses for any signs of wear or damage. Replace any cracked or frayed belts, and tighten any loose hoses. This will help prevent air leaks and ensure efficient operation.
4. Drain moisture from the tank: Air compressors accumulate water in the tank due to the compression process. If left unchecked, this moisture can lead to corrosion and damage to the tank. It’s important to drain the moisture from the tank regularly using the drain valve.
5. Check for leaks: Inspect all fittings, connections, and hoses for any signs of air leaks. Even small leaks can lead to decreased performance and increased energy consumption. If you find any leaks, tighten the connections or replace damaged parts.
Regular maintenance is essential for the longevity and performance of your air compressor. These tips will help keep your compressor running smoothly and prevent costly repairs.
To ensure safety when using an air compressor, here are some important safety tips:
1. Read the manual: Before using your air compressor, thoroughly read it and familiarize yourself with its operation and safety guidelines.
2. Wear appropriate safety gear: When operating an air compressor, always wear safety glasses, ear protection, and proper clothing to protect yourself from flying debris or loud noise.
3. Keep the area clean and well-ventilated: Ensure your work area is clean and free from clutter. Adequate ventilation is also important to prevent the buildup of fumes or exhaust gases.
4. Use proper extension cords: If you need an extension cord, ensure it is the correct gauge for the compressor’s power requirements. Using an inadequate extension cord can lead to overheating and damage.
5. Turn it off when not in use: When you’re finished using the air compressor, always turn it off and unplug it from the power source. This will prevent accidental activation and reduce the risk of injury.
By following these maintenance and safety tips, you can ensure the proper functioning of your air compressor and minimize the risk of accidents or damage.
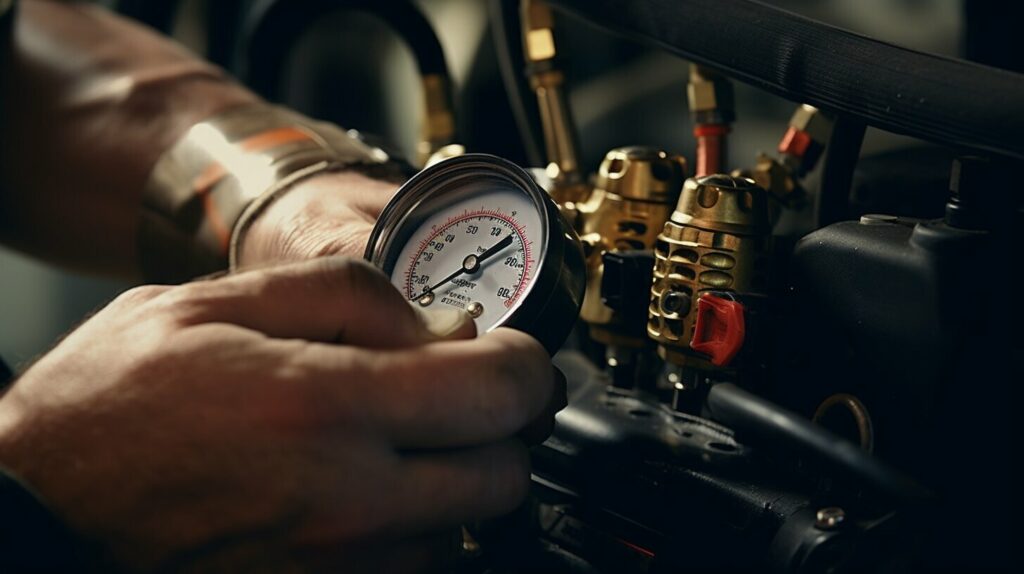
VII. Common Uses of Air Compressors
Air compressors have a wide range of applications in various industries and settings. Here are some common uses of air compressors:
Industrial applications
1. Powering Pneumatic Tools: Air compressors are commonly used in manufacturing and construction industries to power pneumatic tools such as air hammers, drills, wrenches, and nail guns. These tools require compressed air to operate efficiently and effectively.
2. Spray Painting and Finishing: Air compressors are essential for spray painting and finishing applications. They provide the necessary air pressure to atomize paint and evenly distribute it onto surfaces, producing a smooth and professional finish.
3. Manufacturing Processes: Many manufacturing processes rely on air compressors to power equipment and machinery. For example, air compressors are used in pneumatic systems, packaging machines, and control systems.
Home and DIY applications
1. Inflating Tires and Sports Equipment: Air compressors are commonly used to inflate tires, sports equipment, inflatable toys, and air mattresses. They provide a quick and efficient way to fill these items with air.
2. Cleaning and Dusting: Air compressors can be used for cleaning and dusting in DIY projects and home maintenance. They blow compressed air to remove dust and debris from hard-to-reach areas, machinery, and tools.
3. Powering Air Tools: DIY enthusiasts often use air compressors to power various air tools, including nail guns, spray guns, air sanders, and impact wrenches. These tools require compressed air for optimal performance.
Automotive applications
1. Tire Inflation: Air compressors are commonly used in automotive applications to inflate tires. They provide the necessary air pressure to ensure proper tire inflation, which improves fuel efficiency and tire performance.
2. Powering Pneumatic Tools: Automotive repair shops use air compressors to power pneumatic tools such as impact wrenches, ratchets, and sanders. These tools make automotive repairs faster and more efficient.
3. Paint Spraying and Bodywork: Air compressors are essential for automotive painting and bodywork. They power paint spray guns, allowing professionals to apply the paint evenly and achieve a smooth vehicle finish.
These are just a few examples of the wide range of applications for air compressors in various industries and settings. Whether in an industrial environment, doing home DIY projects, or working on your vehicle, an air compressor can greatly enhance your efficiency and productivity.
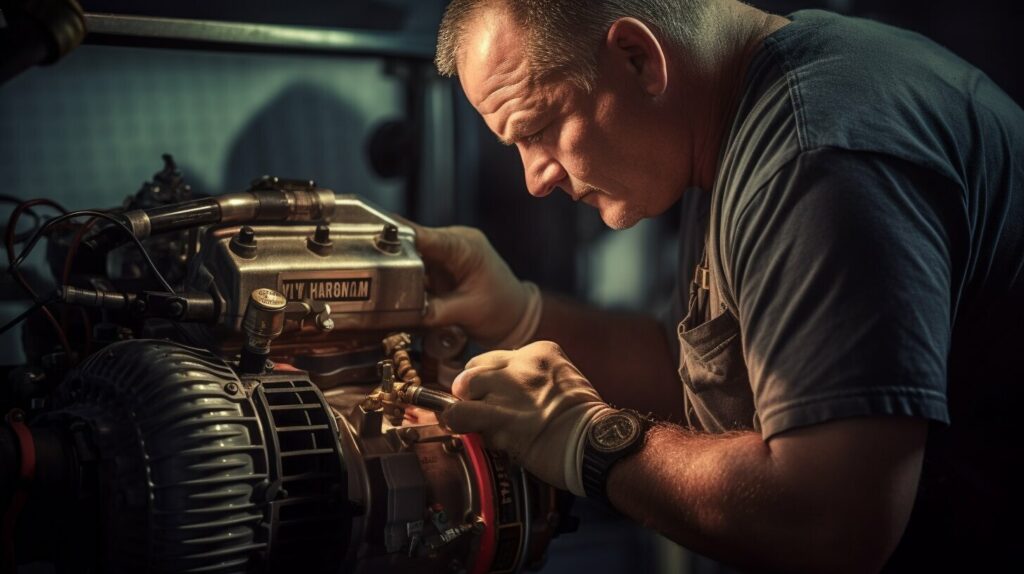
IX. Conclusion
Summary of how an air compressor works
In conclusion, an air compressor is a versatile and essential tool used in various industries and applications. It works by compressing air to a higher pressure, which can then be used to power pneumatic tools, inflate tires, or operate machinery.
The main components of an air compressor include the motor, pump, tank, pressure switch, and various valves and gauges. The motor drives the pump, compressing the air and storing it in the tank. The pressure switch controls the on/off operation of the compressor, while the valves and gauges regulate the airflow and pressure. Understanding how an air compressor works can help you make informed decisions when choosing the right compressor for your needs.
Choosing the right air compressor for your needs
When selecting an air compressor, there are a few factors to consider:
1. Purpose: Determine the primary use of the air compressor, whether it’s for home use, professional applications, or industrial use.
2. Capacity: Consider the volume and pressure requirements of the tools or equipment you use with the compressor.
3. Power source: Decide whether you need an electric or gas-powered compressor based on your access to power outlets and portability needs.
4. Tank size: The tank size will determine the amount of compressed air the compressor can store. Consider the frequency and duration of usage to determine the appropriate tank size.
5. Portability: If you need to move the compressor frequently, consider a portable model with wheels or a compact size.
6. Noise level: Some compressors can be noisy, so if noise is a concern, look for models with noise reduction features or low decibel ratings.
By considering these factors and understanding how an air compressor works, you can make an informed decision and choose the right air compressor for your needs.

X. Frequently Asked Questions
What is an air compressor?
An air compressor is a mechanical device that converts power (usually from an electric motor or an engine) into potential energy stored in compressed air. This compressed air can then be used for various applications, such as powering tools, inflating tires, and operating machinery
How does an air compressor work?
The basic principle behind an air compressor involves three main components: a motor or engine, a compression chamber, and a storage tank. Here’s a simplified step-by-step process: The motor or engine powers the compressor, creating kinetic energy. The kinetic energy is transferred to the compression chamber, where air is drawn in through an intake valve. As the compression chamber decreases in volume, the air is compressed and its pressure increases.
What are the types of air compressors?
Reciprocating compressors: These compressors use pistons and cylinders to compress air. Rotary screw compressors: These compressors use twin screws to compress air. Centrifugal compressors: These compressors use high-speed rotating impellers to compress air. Rotary vane compressors: These compressors use vanes mounted on a rotor to compress air.
What are the uses of an air compressor?
Powering pneumatic tools, such as drills, nail guns, and impact wrenches.
Inflating tires, sports balls, and inflatable toys. Operating machinery, such as paint sprayers, sandblasters, and hydraulic systems. Providing compressed air for HVAC systems, pneumatic controls, and air brakes in vehicles.
Are air compressors noisy
The noise level of an air compressor can vary depending on its design and size. Some air compressors can be relatively quiet, especially those designed for home use or with noise-reducing features. However, larger industrial air compressors may produce higher noise levels. It’s important to consider noise levels when choosing an air compressor for your specific needs.
XI. Additional Resources
For further learning about air compressors, here are some recommended books, websites, and videos that can provide more detailed information on how air compressors work and their applications:
Books:
“Understanding Compressors: Selection, Operation, and Maintenance” by Heinz P. Bloch and John J. Hoefner – This book provides a comprehensive guide to understanding different types of compressors, their operation, selection, and maintenance.
“Air Compressors: A Buyer’s Guide” by Bob Anderson – This book is a practical guide for anyone looking to purchase an air compressor, covering different types of compressors, their features, and factors to consider when choosing the right one for your needs.