Have you ever wondered how to figure out the CFM (cubic feet per minute) requirement for your tools? It can be a bit confusing, but don’t worry, I’ve got you covered!
Determining the CFM requirement for your tools is actually quite simple. CFM refers to the amount of air that a tool needs to operate at its optimal level. To determine this, you’ll first need to know the air consumption of each of your tools. This information is usually provided by the manufacturer and can be found in the tool’s user manual or on its packaging.
Once you have the air consumption for each tool, you’ll want to add them up to get the total CFM requirement for all your tools. This will give you an idea of how much air your compressor needs to be able to provide in order to power all your tools simultaneously. It’s important to remember that your compressor should have a higher CFM rating than the total CFM requirement of your tools to ensure that it can handle the load without any issues.
In this article, we’ll dive deeper into the topic of determining your tools’ CFM requirement. I’ll provide some more detailed steps on how to calculate it and give you some tips on selecting the right compressor for your needs. So, if you’re ready to learn more, keep reading!

Understanding CFM
What is CFM?
CFM stands for cubic feet per minute, which is a unit of measurement used to quantify the airflow rate of a tool or device. It represents the volume of air that can be moved or supplied by the tool in one minute. CFM is an essential metric in determining the compatibility between tools and air compressors, ensuring optimal performance and efficiency.
Why is CFM important?
Understanding the CFM requirement of your tools is crucial for several reasons. Firstly, it ensures that the air compressor you choose can supply enough airflow to meet the demands of your tools. If the CFM rating of the air compressor is too low, it will struggle to deliver sufficient air volume, resulting in decreased tool performance and potential damage.
Secondly, matching the CFM ratings of your tools and air compressor helps to maintain their efficiency. When the CFM capacity of the air compressor matches or exceeds the tool’s requirement, the tool can function optimally without strain. This translates to longer tool lifespan, improved productivity, and reduced energy consumption.
How is CFM measured?
CFM is measured using specialized tools known as flow meters or anemometers. These devices measure the air velocity or flow rate and convert it into cubic feet per minute. To obtain an accurate CFM reading, the tool or device is placed in the airflow path, and the flow meter measures the volume of air moving through it.
Identifying Your Tools’ CFM Requirement
Researching tool requirements
To determine your tools’ CFM requirement, it is essential to research and gather information regarding each tool’s specific needs. This information can usually be found in the tool’s user manual, product specifications, or on the manufacturer’s website.
Consulting tool manuals
Most tools come with a user manual that provides detailed information about their CFM requirement. The manual will typically list the required CFM rating, along with other important specifications. Refer to the manual for accurate CFM information and any additional guidelines or recommendations.
Contacting tool manufacturers
If you are unable to find the CFM requirement for a specific tool, or if you need further clarification, it is recommended to contact the manufacturer directly. The manufacturer’s customer service team should be able to provide you with the necessary information and answer any questions you may have.
Considering Application Factors
Identifying tool usage frequency
Consider how frequently you will be using each tool as it can impact the CFM requirement. Tools used more frequently or for extended periods may require a higher CFM rating to ensure consistent performance. Conversely, tools used infrequently may tolerate a lower CFM rating.
Determining tool size and power
The size and power of a tool can also influence its CFM requirement. Larger tools or those with higher horsepower motors typically require a higher CFM rating to operate effectively. Smaller tools with lower power may have lower CFM requirements.
Accounting for pressure requirements
In addition to CFM, many tools have specific psi (pounds per square inch) requirements. Ensure that the air compressor you choose can supply both the required CFM and the necessary psi for each tool. Failure to meet the recommended pressure can result in reduced tool performance and potential damage.
Calculating CFM Requirements
Determining individual tool requirements
For each tool, determine the specific CFM requirement based on the information gathered from research, tool manuals, or manufacturer contacts. Note down the CFM rating for each tool to have a clear overview of your requirements.
Combining multiple tool requirements
If you have multiple tools that you frequently use simultaneously, you need to consider the CFM requirements of all the tools combined. Add up the individual CFM ratings to determine the total CFM capacity needed from the air compressor.
Considering future tool additions
To future-proof your air compressor choice, consider any potential tool additions or expansions in your collection. It is essential to choose an air compressor with a higher CFM capacity than your current needs to accommodate any future tools you may acquire.
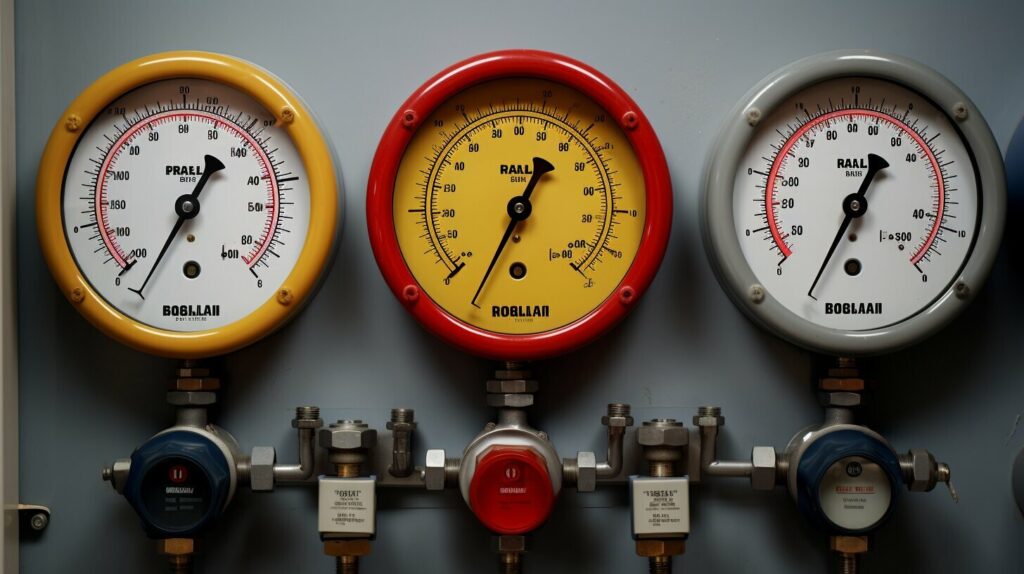
Evaluating Compressor CFM Output
Checking compressor specifications
Once you have determined your tools’ CFM requirements, you need to evaluate the CFM output of the air compressors you are considering. Compare the CFM rating of the air compressor to ensure it can meet or exceed the total CFM requirement of your tools.
Factoring in compressor efficiency
While evaluating the CFM output, it is crucial to consider the efficiency of the air compressor. Some air compressors may have higher CFM ratings but operate at lower efficiencies, resulting in lower actual airflow output. Look for air compressors with high efficiency ratings to ensure optimal performance.
Considering air leakage
Air leakage can significantly affect the actual CFM output of an air compressor. Deteriorated hoses, fittings, or other components can cause air leakage, reducing the effective CFM capacity. Regularly inspect and maintain your air compressor and associated components to minimize air leakage and maximize CFM output.
Matching CFM Ratings
Ensuring tool CFM compatibility
To guarantee optimal tool performance, it is essential to match the CFM rating of each tool with the CFM capacity of the selected air compressor. Ensure that the air compressor can supply the required CFM for each tool without straining or restricting performance.
Selecting a suitable compressor
Based on your total CFM requirements and considering the CFM output and efficiency of various air compressors, select an air compressor that best matches your needs. It should have a sufficient CFM capacity to power all your tools effectively while considering factors such as budget, portability, and noise levels.
Considering Additional Factors
Length and diameter of air hoses
The length and diameter of your air hoses can impact the CFM output from the air compressor to your tools. Longer or narrower hoses can cause a drop in air pressure, reducing the effective CFM reaching the tool. Choose appropriate hose lengths and diameters to minimize pressure loss and maximize CFM delivery.
Air pressure and regulation
In addition to CFM, consider the air pressure requirements of your tools. Ensure that the air compressor can supply the necessary pressure, as indicated by the tool’s specifications. Consider the availability of pressure regulators or adjusters to fine-tune the airflow to each tool’s requirements.
Compressor storage capacity
Consider the storage capacity of the air compressor if you need to transport it to different job sites or if space is limited. Smaller compressors may have lower CFM outputs but offer greater portability. Assess your storage requirements, keeping in mind the total CFM capacity needed for your tools.
Seeking Expert Advice
Consulting professionals
If you are uncertain about determining the CFM requirements for your tools or selecting the appropriate air compressor, seek advice from professionals in the field. Consult with experienced technicians, tool experts, or professionals at your local hardware store for guidance tailored to your specific needs.
Joining online forums
Engaging in online forums or communities dedicated to air compressors and tools can provide valuable insights from experienced individuals. Share your requirements and seek advice from knowledgeable forum members who have encountered similar scenarios. Their expertise can help you make an informed decision.
Attending workshops or classes
Consider attending workshops or classes related to air compressors and tool usage. These educational opportunities provide hands-on training and expert guidance on various aspects, including determining CFM requirements. Gain practical experience and learn from professionals to enhance your understanding and decision-making skills.
Testing CFM Requirements
Using tools with appropriate CFM
Once you have selected an air compressor based on CFM requirements, test the compatibility and performance by using your tools. Ensure that the airflow from the air compressor adequately meets the CFM requirements of each tool. Monitor the tools’ performance and make adjustments if necessary.
Monitoring air supply during use
While using your tools, keep an eye on the air supply from the air compressor. Verify that the tools are receiving a consistent airflow without experiencing any performance issues due to insufficient CFM. If you notice any drop in performance, reevaluate the CFM requirements and the air compressor’s capacity.
Making adjustments if necessary
If you find that the CFM output from your air compressor is not meeting the requirements of your tools, you may need to make adjustments. Consider upgrading to an air compressor with a higher CFM capacity or reevaluating your tool selection to ensure compatibility with the available CFM output.
Conclusion
Determining the CFM requirements of your tools is essential for maintaining their performance, efficiency, and longevity. By researching tool requirements, considering application factors, calculating CFM requirements, evaluating compressor CFM output, matching CFM ratings, and considering additional factors, you can optimize the tool-air compressor pairing. Seek expert advice when needed, test CFM requirements in practice, and ensure that your tools receive sufficient airflow to operate at their best. This understanding and attention to CFM will ensure that you have a successful and efficient toolkit setup.