Today we’ll be talking about whether or not an air compressor can explode. You’ll learn about the possible causes of air compressor explosions and what precautions you can take to prevent them. We’ll also discuss how to safely use and maintain your air compressor to minimize the risk of an explosion.
So, let’s get started and find out if air compressors can be a hazard!

Understanding Air Compressors
An air compressor is a versatile and powerful tool in various industries and applications. It converts power from an electric motor or gasoline engine into stored pressurized air.
This pressurized air can be used for various tasks, such as inflating tires, powering pneumatic tools, and even providing air for diving equipment.
How does an air compressor work?
The basic principle behind an air compressor is fairly simple. It starts with an intake valve that allows atmospheric air to enter the compressor’s chamber.
Once inside, the air is compressed by reducing the volume of the chamber, which increases the pressure exerted on the air molecules. This compressed air is stored in a tank or released directly.
Different types of air compressors
There are several types of air compressors available, each with its own advantages and limitations. The most common types include:
Reciprocating air compressors: These compressors use pistons and cylinder arrangements to compress air. They are known for their high-pressure capabilities and efficiency.
Rotary screw air compressors: These compressors use two interlocking helical rotors to compress air. They are commonly used in industrial settings for their reliability and continuous-duty operation.
Centrifugal air compressors use a rotating impeller to accelerate and compress air. They are ideal for large-scale applications requiring high volumes of compressed air.
Scroll air compressors: These compressors use two spiral-shaped scrolls to compress air. They are compact, quiet, and energy-efficient, making them suitable for residential and smaller commercial applications.
Each type of air compressor has its unique characteristics, and the choice depends on the specific requirements of the task at hand.
Potential Risks and Safety Precautions
While air compressors offer a wide range of benefits, it is important to be aware of the potential risks associated with their use. Understanding these risks and implementing appropriate safety precautions is crucial to prevent accidents and injuries.
Overview of potential dangers
Air compressors can pose various dangers, including:
Explosion: The pressurized air within the compressor and tank can potentially lead to explosions if improperly maintained or safety precautions are not followed.
Overheating: Continuous operation of an air compressor can cause it to overheat, leading to mechanical failures and potential hazards.
High-pressure release: Accidental release of high-pressure air can cause severe injuries, including cuts, bruises, and even loss of limbs.
Fire hazards: Air compressors have electrical components and generate heat, which can increase the risk of electrical fires if not properly maintained.
Can an air compressor explode?
While explosions involving air compressors are relatively rare, they can occur under specific circumstances. However, it is important to note that not all air compressors are at the same risk level.
The probability of an air compressor exploding depends on various factors, including the quality and maintenance of the compressor, operating conditions, the presence of flammable materials, and improper usage or modifications.
Common causes of air compressor explosions
Air compressor explosions can be caused by a combination of factors, including:
Overheating: If an air compressor runs continuously without proper cooling or maintenance, it can overheat and eventually lead to an explosion.
Mechanical failures: Poor maintenance, worn-out parts, or faulty safety features can contribute to mechanical failures that may result in an explosion.
Pressure build-up: If an air compressor operates at a pressure higher than its maximum capacity, it can lead to excessive pressure build-up and potential explosion.
Inadequate ventilation: Inadequate ventilation in the area where the air compressor is operating can cause heat and pressure to accumulate, increasing the risk of an explosion.
Safety precautions to prevent explosions
To minimize the risk of an air compressor explosion, it is essential to implement the following safety precautions:
Regular maintenance: Proper maintenance, including regular inspection, cleaning, and lubrication, is crucial to ensure the safe operation of an air compressor and minimize the risk of explosions.
Replacement of worn-out parts: Regularly inspect and replace any worn-out or damaged parts to maintain the integrity and safety of the air compressor.
Adequate ventilation: Ensure that the area where the air compressor is operated has proper ventilation to prevent the accumulation of heat and pressure.
Operating within recommended limits: Always operate the air compressor within its recommended pressure limits and avoid exceeding its maximum capacity.

Signs of Possible Explosion
To detect potential issues with an air compressor and minimize the risk of an explosion, it is important to be aware of the following signs:
Unusual noises or vibrations
Unusual noises, such as grinding or rattling, can indicate mechanical problems within the air compressor. Excessive vibrations can also signify impending failure, which may lead to an explosion if not addressed promptly.
Leaking of air or oil
Air or oil leaks from the air compressor can indicate potential issues, such as faulty seals, loose fittings, or damaged components. These leaks can contribute to pressure build-up and increase the risk of an explosion.
Overheating or excessive pressure
If an air compressor becomes unusually hot or operates at a higher pressure than usual, it may indicate impending failure. Overheating or excessive pressure can weaken the components of the air compressor and make it more susceptible to explosions.
Sudden shutdowns or malfunctions
Frequent shutdowns or malfunctions of the air compressor, such as sudden loss of power or irregular operation, can indicate underlying issues that must be addressed. Ignoring these signs can lead to mechanical failures and potentially result in an explosion.
Factors Affecting the Risk of Explosion
Several factors can influence the risk of an air compressor explosion. Being aware of these factors can help prevent accidents and ensure the safe use of air compressors.
Quality and maintenance of the air compressor
The air compressor’s quality and regular maintenance play a significant role in reducing the risk of an explosion. Investing in a reputable brand and conducting regular inspections, cleaning, lubrication, and replacing worn-out parts are crucial to ensure the safe operation of the compressor.
Operating conditions
The conditions under which an air compressor operates can affect its risk of explosion. Factors such as ambient temperature, humidity, and the presence of dust or other contaminants can impact the performance and safety of the air compressor.
Presence of flammable materials
Operating an air compressor in an area with flammable materials significantly increases the risk of an explosion. It is crucial to keep the compressor away from any potential ignition sources and ensure that the surrounding environment is free of flammable substances.
Improper usage or modifications
Using an air compressor for purposes other than its intended applications or making unauthorized modifications can increase the risk of an explosion. Following the manufacturer’s guidelines and refraining from any modifications that may compromise the safety and integrity of the compressor is essential.
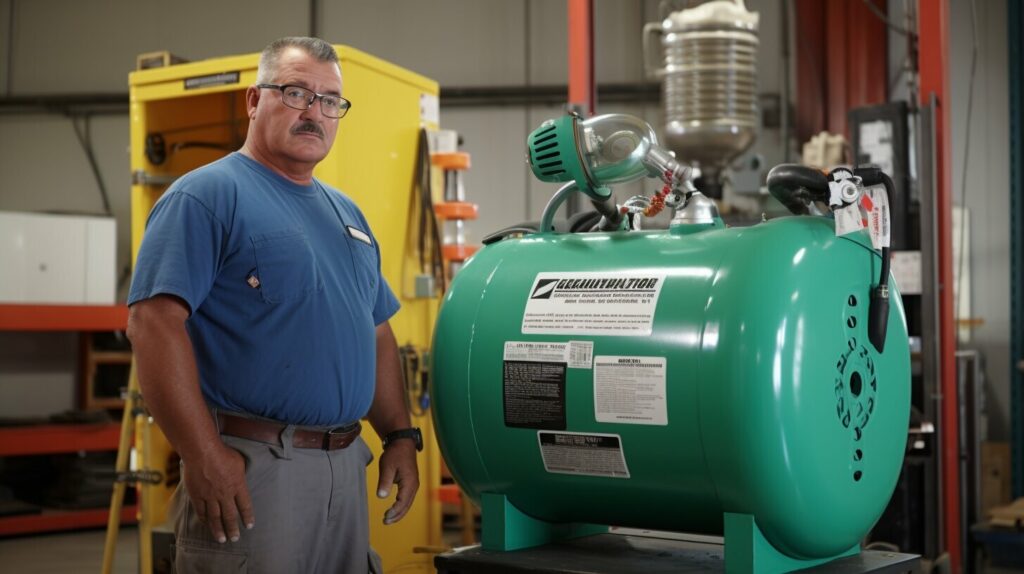
Preventive Maintenance and Inspections
Regular maintenance and inspections are key to ensuring the safe operation of an air compressor and minimizing the risk of explosions. Here are some important steps to include in a regular inspection checklist:
Cleaning and lubrication
Regularly clean the air compressor to remove dust, debris, and potential obstructions. Lubricate moving parts as the manufacturer recommends to reduce friction and prevent premature wear.
Replacement of worn-out parts
Inspect all air compressor components for signs of wear, damage, or corrosion. Replace any worn-out parts promptly to ensure the integrity and safety of the compressor.
Ensuring proper ventilation
Check that the area where the air compressor is operated has adequate ventilation to prevent the accumulation of heat and pressure. Ensure that the compressor’s cooling system is functioning properly and is free from obstructions.
Proper Use and Handling
The proper use and handling of an air compressor are crucial to prevent accidents and ensure the safety of both the users and the equipment. Consider the following guidelines:
Following the manufacturer’s guidelines
Read and understand the manufacturer’s instructions and guidelines before operating the air compressor. Adhere to the recommended pressure limits, operating procedures, and maintenance requirements to ensure safe and efficient operation.
Correct storage and transport
Store and transport the air compressor in a secure and well-ventilated area. Avoid exposing the compressor to extreme temperatures, moisture, or direct sunlight, as these factors can affect its performance and safety.
Safety measures during operation
When operating the air compressor, wear appropriate personal protective equipment, such as safety glasses, gloves, and hearing protection. Keep the compressor away from flammable substances, open flames, or sparks, and never smoke or use the compressor in areas where flammable gases or vapors are present.
Proper handling of compressed air
Always handle and direct compressed air with caution. Avoid pointing the air stream at yourself or others, as it can cause severe injuries. Do not use compressed air to clean clothes, skin, or equipment. Use appropriate attachment tools and accessories designed specifically for compressed air applications.
Emergency Procedures
While thorough safety measures aim to prevent air compressor explosions, it is essential to be prepared for emergencies. In the event of an explosion or any other related incident, follow these emergency procedures:
Immediate actions in case of an explosion
If an air compressor explodes, the priority is to ensure personal safety. Leave the area immediately and take cover in a safe location. Please do not attempt to extinguish any resulting fires unless it is safe.
First aid for injuries
In case of injuries caused by an air compressor explosion, administer first aid immediately. Call for medical assistance and provide any necessary assistance until professional help arrives.
Emergency shutdown and evacuation
In case of an air compressor explosion, activate any emergency shutdown procedures and evacuate the area. Follow designated evacuation routes and assemble in designated safe zones until the area is deemed safe.
Legal and Regulatory Requirements
Various legal and regulatory requirements govern the safe use and operation of air compressors, ensuring the protection of workers and the environment. Some important regulations include:
Occupational Safety and Health Administration (OSHA)
OSHA has established safety regulations and guidelines for using air compressors in the workplace. These regulations cover general safety requirements, hazard communication, and personal protective equipment.
Industry-specific regulations
Different industries may have specific regulations and standards related to the safe use of air compressors. Familiarizing yourself with industry-specific requirements and ensuring compliance to maintain a safe working environment is essential.
Compliance and record-keeping
Maintaining compliance with relevant safety regulations requires proper record-keeping. Keep records of regular inspections, maintenance activities, and any training provided to employees regarding the safe operation of air compressors.
Case Studies and Lessons Learned
Analyzing real-life incidents and learning from them is valuable to better understand the risks associated with air compressors. Here are a few examples of air compressor explosions and the lessons we can derive from them:
Real-life incidents of air compressor explosions
In 2018, an air compressor explosion at a manufacturing facility caused significant damage and injuries. The explosion was attributed to a worn-out pressure relief valve that failed to release excess pressure. Another incident involved an air compressor explosion due to improper maintenance and the use of incompatible lubricants.
Analysis of causes and consequences
In both incidents, inadequate maintenance and failure to follow recommended guidelines were the primary causes of the explosions. The consequences included property damage, injuries to personnel, and disruption of operations.
Important takeaways for prevention
These incidents emphasize the importance of regular maintenance, proper inspections, and following the manufacturer’s guidelines. Organizations can significantly reduce the risk of air compressor explosions by ensuring compliance with safety regulations and industry best practices.
Conclusion
While air compressors provide valuable functionality, it is crucial to be aware of the potential risks associated with their use.
By understanding the causes of air compressor explosions and implementing necessary safety precautions, you can ensure the safe operation of air compressors.
Regular maintenance, inspections, and following manufacturer’s guidelines are key to minimizing the risk of explosions and maintaining a safe working environment.
Remember, continuous learning and improvement in air compressor safety practices are crucial to ensure the well-being of operators and equipment.